The Importance of Plastic Injection Tooling in Modern Manufacturing
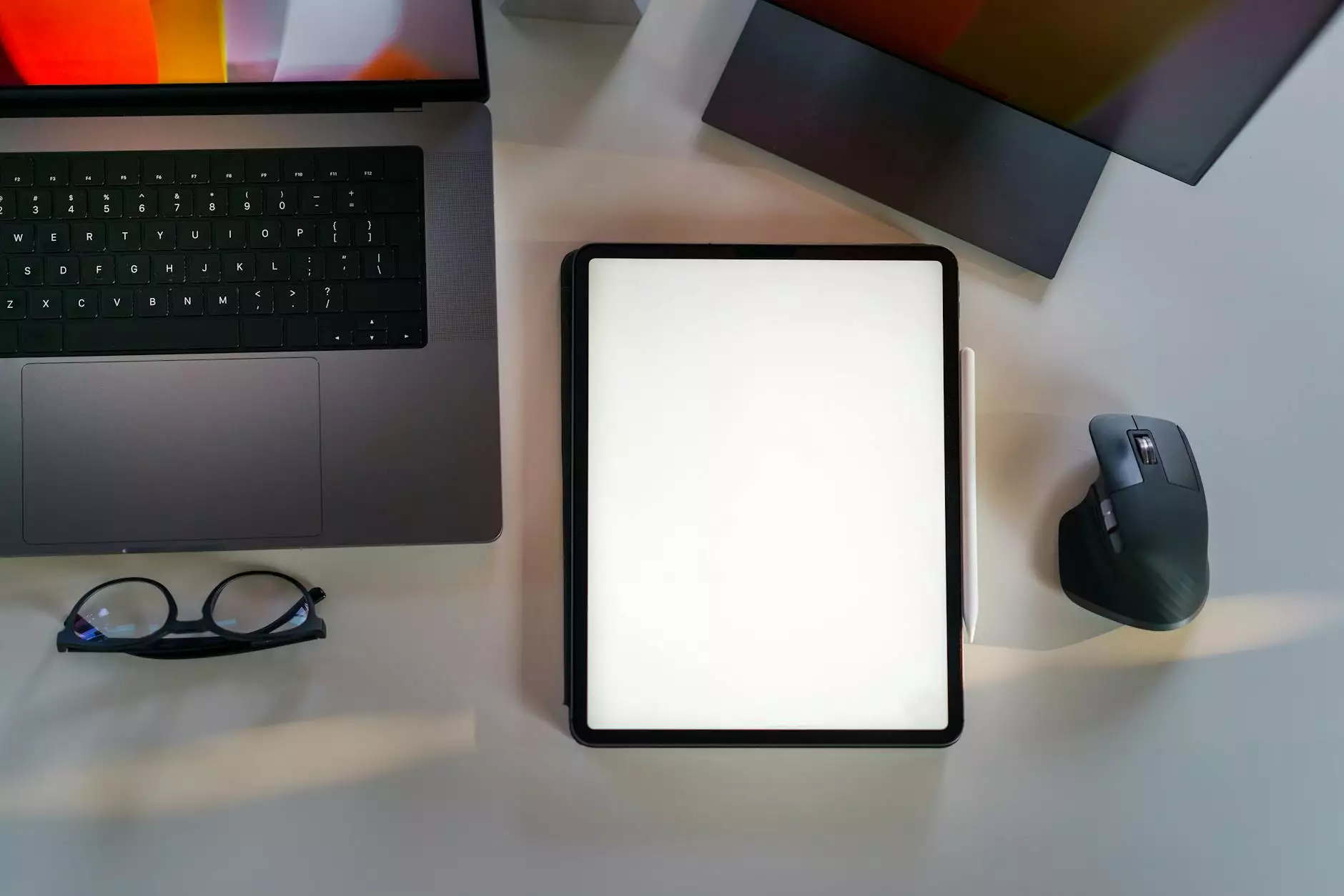
In today's highly competitive market, businesses must leverage innovative manufacturing processes to enhance productivity, reduce costs, and improve product quality. One such crucial process is plastic injection tooling. This technology has revolutionized the way manufacturers produce plastic parts and components, making it a key player in various industries, from automotive to consumer electronics. In this article, we will explore the intricacies of plastic injection tooling, its benefits, its applications, and how it can elevate your business operations.
Understanding Plastic Injection Tooling
Plastic injection tooling refers to the creation of molds that are used in the plastic injection molding process. This process involves injecting molten plastic into a mold to create a specific shape. The efficiency and precision of this process heavily rely on the quality of the tooling. High-quality molds ensure that the final products are produced with accuracy and consistency, which are essential for maintaining a competitive edge in the market.
The Process of Plastic Injection Tooling
The plastic injection tooling process can be broken down into several stages:
- Designing the Mold: This first step involves creating a detailed design of the mold using computer-aided design (CAD) software. Designers consider factors such as the geometry of the part, the type of material, and the production volume.
- Material Selection: The choice of material for the mold is critical. Common materials include steel and aluminum, each with its own set of advantages and disadvantages.
- Manufacturing the Mold: The mold is produced using precision machining techniques. This stage requires skilled operators who can ensure that the mold meets the exact specifications.
- Testing: Once the mold is manufactured, it undergoes rigorous testing to ensure it produces parts accurately and efficiently. Any modifications needed are made at this stage.
- Production: After successful testing, the mold is ready for production, where it will be used repeatedly to create high-quality plastic parts.
Benefits of Using Plastic Injection Tooling
The advantages of incorporating plastic injection tooling into your manufacturing processes are numerous. Here are some key benefits:
- High Precision: Injection molding provides exceptional precision, making it ideal for creating complex parts with intricate details.
- Cost-Effectiveness: Although the initial investment in tooling can be high, the long-term savings on production costs and material waste make it a cost-effective solution.
- Scalability: Once the molds are created, producing large quantities of parts becomes easy and efficient, allowing businesses to scale production quickly.
- Versatility: Plastic injection tooling can be used for a wide range of materials, including thermoplastics and thermosetting plastics, making it suitable for various applications.
- Enhanced Strength and Durability: Parts produced using high-quality molds and modern plastic materials are often stronger and more durable than those produced through other methods.
Applications of Plastic Injection Tooling
The applications of plastic injection tooling are vast and varied. Here, we highlight some key industries and their specific uses:
1. Automotive Industry
In the automotive sector, plastic parts are used extensively for interior components, exterior trim, and even critical systems such as fuel systems and electrical housings. The precision offered by injection molding ensures that these components fit seamlessly and perform reliably under various conditions.
2. Consumer Electronics
The production of consumer electronics, from smartphones to home appliances, relies heavily on plastic injection tooling. The ability to create lightweight yet durable casings and components is crucial in this fast-paced industry.
3. Medical Devices
In the medical field, precision and sterility are paramount. Plastic injection tooling allows for the mass production of complex medical devices, such as syringes, inhalers, and surgical tools, while maintaining the strict standards required in healthcare.
4. Packaging Industry
The packaging industry benefits significantly from plastic injection molding, with applications including bottles, containers, and customized packaging solutions that require both durability and aesthetic appeal.
Choosing the Right Plastic Injection Tooling Partner
When considering plastic injection tooling for your business, selecting the right partner is crucial. Here are some factors to consider:
- Experience: Choose a company with a proven track record in plastic injection tooling and molding.
- Technology: Ensure that the partner employs the latest technologies and methodologies in their tooling process.
- Quality Assurance: Look for partners that prioritize quality control throughout the manufacturing process.
- Customer Support: Reliable customer support can make a significant difference in addressing any issues that may arise during production.
- Reputation: Research reviews and testimonials from other clients to gauge their satisfaction with the tooling provider's services.
Trends in Plastic Injection Tooling
The landscape of plastic injection tooling is continuously evolving. Here are some trends shaping the future of this industry:
1. Sustainable Practices
As environmental concerns grow, manufacturers are looking for sustainable practices in injection molding, including the use of recycled materials and energy-efficient processes.
2. Advanced Materials
The development of advanced polymers and composites is enabling manufacturers to create lighter and stronger products, broadening the applications of plastic injection molding.
3. Automation and Smart Manufacturing
Automation technologies are streamlining the plastic injection tooling process, enhancing efficiency and reducing labor costs. Smart manufacturing practices are enabling real-time monitoring and adjustments for optimal production performance.
Conclusion
In summary, plastic injection tooling is an essential component of modern manufacturing that brings numerous benefits to various industries. Its high precision, cost-effectiveness, and versatility make it a valuable asset for businesses looking to enhance their production capabilities. By choosing the right tooling partner and staying abreast of industry trends, companies can ensure that they remain competitive and make the most of the opportunities presented by this dynamic manufacturing process.
If you are interested in exploring the possibilities of plastic injection tooling for your business, don’t hesitate to reach out to industry leaders like Deep Mould. Their expertise in metal fabrication and commitment to quality can help you meet your manufacturing needs efficiently and effectively.